|
|
|
|
|
|
|
|
|
|
|
|
|
|
The quarter sawn White Oak is placed in a heated
room for 7 to 10 days to bring the wood moisture down to 9%
to 10%..... because this entry will reside in a fairly arid
climate in Northern California
|
|
The hand picked White Oak is now at 12% moisture
content
I'll start machining the wood in about a week
|
|
Here are the ends of the quarter sawn White oak
...... notice closeness of the annual growth rings
|
|
Here is a rejected piece of White oak that has cell
collapse. Notice that the cracks do not show until you cut
into the board
|
|
|
Click
on
|
Any
|
Image to
Enlarge
|
|
|
|
|
|
|
|
|
|
|
|
|
|
|
|
|
The rough lumber for the entry door is
selected
|
|
..... and all the rough pieces are chosen and then
off to the saws to be cut up.
|
|
Then .... each piece is joined on its face and made
perfectly flat to be run through the planer
|
|
Here are the "center" pieces of the entry door after
being joined ..... allowed to "relax" before
planing.
|
|
|
|
|
|
|
|
|
|
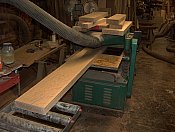
|
|
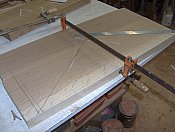
|
|
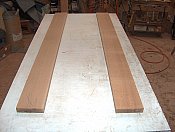
|
Here are the styles for the entry door after being
flattened on one side.
|
|
They are the planed to a parallel thickness
|
|
This is the top of the door being laid out for the
chevron lite opening
|
|
here are the two 7"+ door styles of White Oak ..... they
each weigh over 40 lbs each ....... I mean solid wood !!
|
|
|
|
|
|
|
|
|
|
|
|
|
|
|
Here are some of the Medullary Rays that appear in
White Oak when the wood is milled perfectly
vertical
|
|
This is some of the most beautiful White Oak that I
have ever seen
|
|
Here are he pieces for the sidelights, after being
joined and allowed to settle down
|
|
|
|
|
Click
on
|
Any
|
Image to
Enlarge
|
|
|
|
|
|
|
|
|
|
|
|
|
|
|
|
|
The "heels" are glued together and then surface
sanded to 1-3/4" thick
|
|
The "heels" are are the surface sanded because the
can not be planed due to reversing grain
|
|
The to "lite" of the door has a stepped style that
is very complex to create ..... the final step is hand cut
with a finishing dozuki dovetail saw
|
|
Here are the two stepped heel ready to do a splined
mortise with the top angled rail
|
|
|
|
|
|
|
|
|
|
|
|
|
|
|
The top "chevron" is cut out of the top
rail
|
|
It is the detailed with preliminary routers
|
|
...... and then completed with hand tools
|
|
The top piece is stepped in 2"
|
|
|
|
|
|
|
|
\
|
|
|
|
|
|
|
Here is a view of the header after mortising for the
splined tennons
|
|
Here is the door with the fitted horizontal
rails
|
|
The the vertical styles are each fitted and refitted
for an exact fit ...... this is a view of the
outside
|
|
Here is a view of the inside after all of the pieces
have been fitted and shaped
|
|
|
|
|
|
|
|
|
|
|
|
|
|
|
Here is a close-up of a view of the inside
|
|
Here is a clasp of a sidelight
|
|
The figure in this White Oak is amazing
|
|
,,,,,,,,, and the view just gets better and
better
|
|
|
|
|
|
|
|
|
|
|
|
|
|
|
Here is the first sidelight glued up, flattened, and
in clamps
|
|
....... here is the entry door in clamps
|
|
all of he excess glue is cleaned and the corners are
cleaned with a toothbrush
|
|
... here is the second sidelight in clamps
|
|
|
|
|
|
|
|
|
|
|
|
|
|
|
the entry door ... curing
|
|
Here are the 2 sidelights and the entry door in
clamps and they will be allowed to cure for at least 72
hrs
|
|
Here is the beautiful entrance door ..... just out
of clamps
|
|
Here are the two sidelights just out of
clamps
|
|
|
|
|
|
|
|
|
|
|
|
|
|
|
Here is a close-up of the top chevron lite which
will have gold mirrored solar bronze glass
|
|
All of the molded edges must be hand sanded
|
|
....... and sanded
|
|
........ and hand sanded
|
|
|
|
|
|
|
|
|
|
|
|
|
|
|
Here are some of the beautiful White Oak raised
panels ...... they are 1-3/8" thick
|
|
Here are the two sidelights ..... good news .......
they match !!
|
|
The door is mortised for 4 hinges and I brand it
while I'm there
|
|
The door is being bored for the lock set and dead
bolt
|
|
|
|
|
|
|
|
|
|
|
|
|
|
|
It fits!!
|
|
The panels are a full 1-3/8" thick and raised on
both sides
|
|
Here the panels receive the first of four coats of
my varnish oil oil
|
|
Check out the grain ...... amazing !
|
|
|
|
|
|
|
|
|
|
|
|
|
|
|
Each and every stop is soaked in my oil at least 4
different times.
|
|
FINALLY ....... the door receives its' first coat of
varnish oil
|
|
Here is a close-up of the inside top
|
|
Here's my "baby" curing for at least 72 hrs
|
|
|
|
|
|
|
|
|
|
|
|
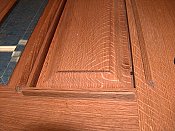
|
|
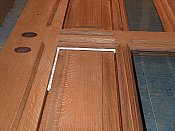
|
Here are the sidelights being oiled before the
panels are placed in the units.
|
|
Here are the beveled glass units
|
|
Please note that all of my panels "float" within their
frame. The panel can then move without tearing itself
apart
|
|
The panels are then caulked with a flexible siliconized
latex caulk that turns clear ...... but it is never
seen.
|
|
|
|
|
|
|
|
|
|
|
|
|
|
|
Here is a preview of the door.
The upper peaked light actually mimics the house roof
line.
|
|
Here is the beveled glass installed
|
|
The upper unit is actual a thermal unit that has a
bronze mirror coating on the outside piece of the
unit
|
|
Here is a close-up of the "jog". I decided to apply
a raised molding which I designed. It's a surprise for the
clients!!
|
|
|
|
|
|
|
|
|
|
|
|
|
|
|
Here the bronze hinges are mortised into the White
oak jambs
|
|
Here is a sidelight ....... about to receive the
stops ...... ALL STOPS are attached with stainless steel
fasteners
|
|
One down .... one to go !
|
|
Most of our exceptional fabricated glass products
have been constructed by Thermal Sun Glass of Santa Rosa,
CA
|
|
|
|
|
|
|
|
|
|
|
|
|
|
|
Here is the entry door hung in a solid White Oak
jamb ...... with 4 ball-bearing bronze hinge
|
|
I provide the jambs "long" so the owner can fit it
to their project. Notice the weather-stripping
|
|
My jambs have a vinyl/foam European style weather
stripping. It is kerfed directly into the jamb ... and easy
to replace
|
|
My jambs are assemble with 4 inch screws ...... no
staples or nails ....... notice the outside of the jamb has
also been sealed with my varnish oil ......!
|
|
|
|
|
|
|
|
|
|
|
|
|
|
|