|
|
|
|
|
|
...........................
|
The project begins. All of the pieces of the door
are roughed out then allowed to "relax" and settle
down
|
|
We ALL
wait in eager anticipation
to watch this door come into reality!!
|
|
Here is a view of the quality of the close grain of
the White Oak
|
|
And some of it is so fine grained ... it is just
amazing quality.
|
|
|
|
|
|
|
|
|
|
|
|
|
|
|
The rough lumber is joined and the surfaced
|
|
and then joined on edge
|
|
some of the wood has so many medullary rays that it
must be surface sanded
|
|
Here are the pieces for the short mullions
|
|
|
|
|
|
|
|
|
|
|
|
|
|
|
Here is the door "frame"
|
|
The long mullions are first cut to length and the
coped on the ends
|
|
The long vertical mullions are then fit in their
place
|
|
then ...... one by one the short mullions are fitted
in their place
|
|
|
|
|
|
|
|
|
|
|
|
|
|
|
Each one of these 16 mullions are fit to fit
perfectly
|
|
It took 5-1/4hrs to "cope" the 16 short mullions
..... but the fit is worth it !!
|
|
this is the coping process ..... now I will finish
the "sticking" process by molding the edges
........
|
|
Here is a completed mullion
|
|
|
|
|
|
|
|
|
|
|
|
|
|
|
These 16 pieces took 6 hours to complete
|
|
The door has to be assembled from the inside
out
|
|
Clamping of this door is am interesting array of 5
different types of clamps
|
|
spacer blocks are placed between the mullions so
that pressure can be exerted to clamp the joints during
curing
|
|
|
|
|
|
|
|
|
|
|
|
|
|
|
Here is the door ........ in all its' glory .......
now the cleaning of all the excessive glue is
removed
|
|
the nice fitting joints are cleaned with water and a
toothbrush.
It took 4 hrs to assemble and clean this beautiful
door
|
|
the glue I use is a 2 part urea resin , which starts
out water soluble and within hours becomes water proof and
takes up to 72 hrs to cure and harden
|
|
Here is he "raw" door out of clamps ......... it has
very nice proportions.
|
|
|
|
|
|
|
|
|
|
|
|
|
|
|
Each and every inch of the molded detail is hand
sanded 3 times with 3 different grits of sandpaper
|
|
Then both sides are finish sanded
|
|
and finish sanded ...... to 220 grit ..... which is
furniture grade !!
|
|
When I prehang the door, I back bevel the leading
edge to 2deg for ease of opening
|
|
|
|
|
|
|
|
|
|
|
|
|
|
|
Since this door will weigh a hefty amount ......I
use 4 hinges and place two of them toward the top of the
door, since 85% downward force pull at the top of the door
and jamb.
|
|
ahhhhh ...... all of the hinges are mortised and I
sign the door
|
|
I was working on my roof the other day ......... and
took this picture of the first coat of oil soaking into the
door.
|
|
Here is "The Cape" after the first coat of varnish
oil ........ The door will cure for 4 days till the next, of
4, coats.
|
|
|
|
|
|
|
|
|
|
|
|
|
|
|
Here are some "scraps" from the door wood ...... I
plane it down and make the glass stops from this
wood.
|
|
I use "scraps" from the door stock so that the stops
match the wood in the door ..... here are the stops ready
for sanding and oil
|
|
The jambs are made, kerfed for weather-stripping,
and the mortised for the hinges
|
|
here is a view of the jambs ........ I have 2 hinges
at the top of the jamb because of the weight of the
door
|
|
|
|
|
|
|
|
|
|
|
|
|
|
|
The jambs are sanded and prepped for oil
|
|
Here the door receives its' 3rd coat
|
|
The jambs have 3 coats of oil and are sealed on both
sides
|
|
Here are the short stops, curing after being soaked
in oil
|
|
|
|
|
|
|
|
|
|
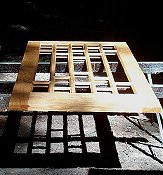
|
|
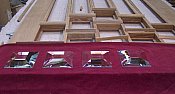
|
|
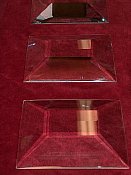
|
The long stops cure at least 72 hrs between
coats
|
|
Here is the 4th and last coat of varnish oil
|
|
We are still waiting for most of the glass ........ but
we have stared cutting the 186 individual miters in this
door
|
|
Here are some pictures of the 3/4" thick, hand beveled,
Diamante Starfire
|
|
|
|
|
|
|
|
|
|
|
|
|
|
|
Here is a view of the Jewel in the door
|
|
Here I am boring for the lockset and deadbolt and
then will oil all raw wood
|
|
a sneak peek
|
|
Here we are placing the weather stripping in the
White Oak jambs
|
|
|
|
|
|
|
|
|
|
|
|
|
|
|
while were waiting on the glass we start the
shipping crate....... it is screwed together, and very
solid
|
|
the door will be wrapped in plastic and rest on 2
different types of foam
|
|
Here is an end view the the solid White Oak, 1-1/2"
jamb with weather-stripping
|
|
....... here I am putting the jamb together .......
hinge side first
|
|
|
|
|
|
|
|
|
|
|
|
|
|
|
Here is the door prehung in the jamb ......... then
I disassemble the jamb and ready it for shipment
|
|
here is he jamb wrapped and ready for its' trip to
Cape Cod
|
|
Here are the beveled units ready for
installation
|
|
Here the glass is set into the rubber spacers and
all the stops are ready to be attached
|
|
|
|
|
|
|
|
|
|
|
|
|
|
|
Each unit is set in a special caulking that turns
clear when dry
|
|
All of the glass is "bedded" and the stops are
attached with stainless steel fasteners
|
|
Another view
|
|
Here the finished door is first wrapped in plastic
before placed in its' shipping case
|
|
|
|
|
|
|
|
|
|
|
|
|
|
|
Here is the door, jamb, and hinges are placed in the
shipping case
|
|
The door is sandwiched between walls of
foam
|
|
|
|
Here is one of the hand beveled Starfire jewels
permanently installed in the door
|
|
|
|
|
|
|
|
|
|
|
|
Click
Here to View the Installation of The
Cape
|
|
|
|
|
The last wall is screwed on to the frame and the door is
ready to make its journey across the country
|
|
|
|
|
|
|
|
|
|
|
|
|
|
|
|
|
|
|